Formnext 2021: Fraunhofer IPT, FH Aachen und Präwest stellen neues Wasserstoff-Brennkammer-Design im 3D-Druck her
Wasserstoff wird zu einem immer wichtigeren Energieträger gegen den Klimawandel. Die Wasserstoffverbrennung setzt zwar kein Kohlendioxid frei, doch was kaum jemand weiß: Es entstehen mehr Stickoxide (NOx) als bei der Verbrennung fossiler Brennstoffe. In einem gemeinsamen Forschungsprojekt haben die FH Aachen und das Fraunhofer-Institut für Produktionstechnologie IPT aus Aachen sowie die Präwest Präzisionswerkstätten GmbH & Co. KG aus Bremen mit einem additiven Fertigungsverfahren eine Wasserstoff-Brennkammer in einem neuen Design hergestellt, das den Ausstoß von Stickoxiden deutlich senken kann. Diesen Prototypen stellen die Partner nun auf der Formnext, der Fachmesse für additive Fertigung und industriellen 3D-Druck, dem Messepublikum vor.
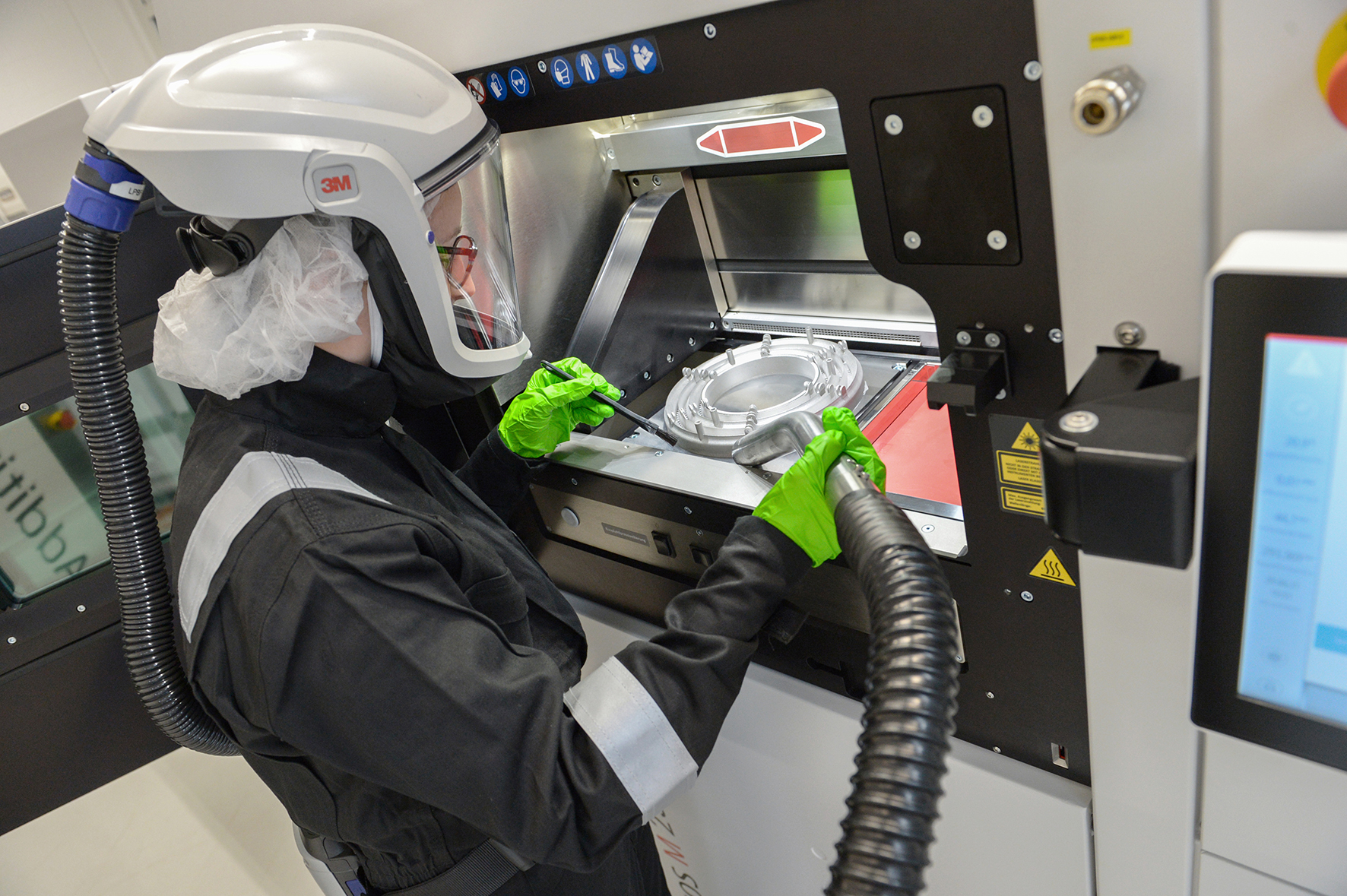
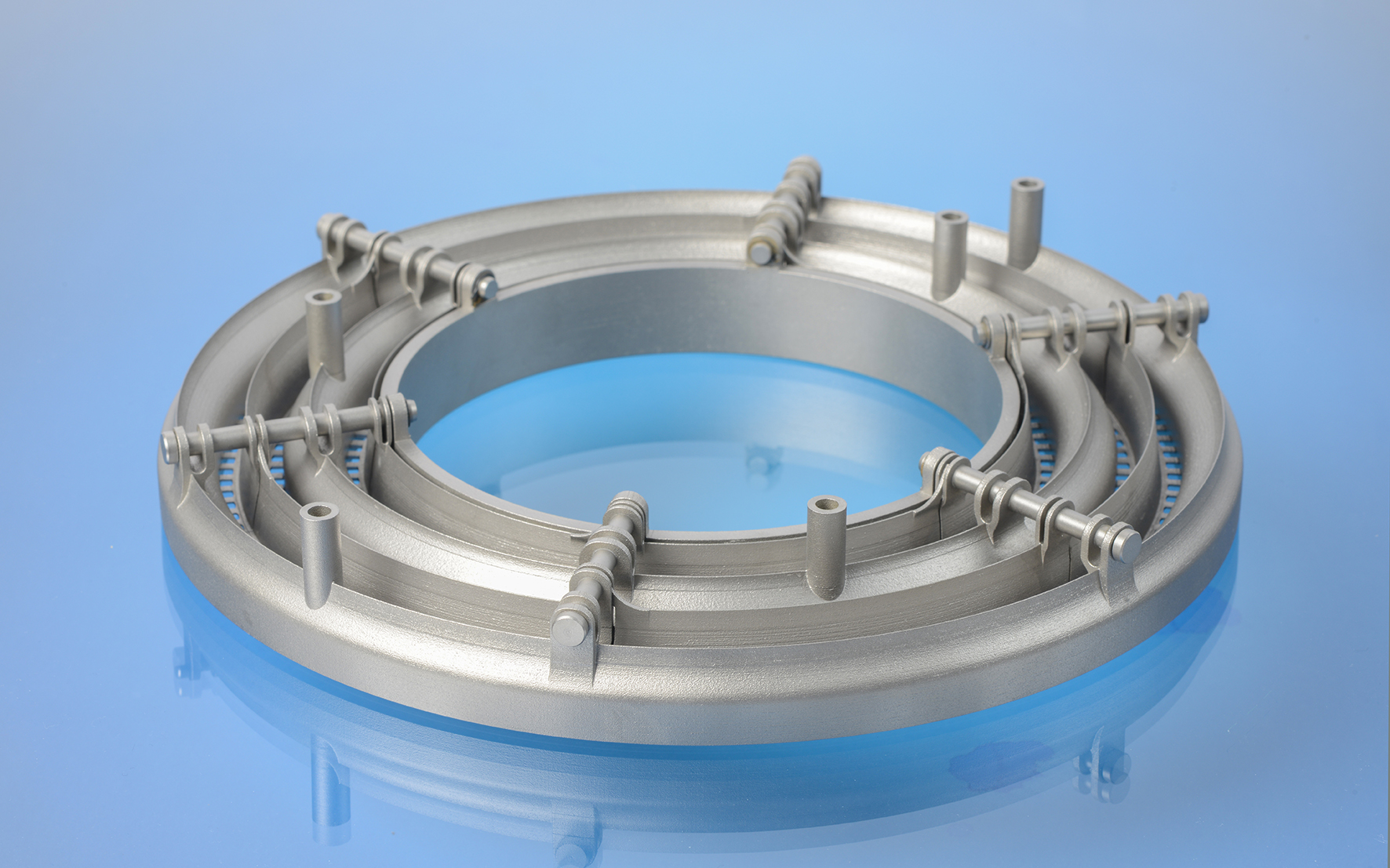
Das Design der Wasserstoff-Brennkammer, die die Partner auf der Messe zeigen, unterstützt das MicroMix-Brennverfahren (MMX), entwickelt von Prof. Dr. Harald Funke am Fachbereich Luft- und Raumfahrttechnik der FH Aachen, das im Oktober mit dem Forschungspreis 2021 der FH Aachen ausgezeichnet wurde. Dieses Verfahren setzt im Vergleich zu herkömmlichen Verbrennungsprozessen mit einigen großen Flammen auf eine Vielzahl kleinerer Flammen. Die MMX-Brennkammer ist so konzipiert, dass das Gas sich optimal mit der zugeführten Luft vermischt und mit geringerer NOx-Bildung verbrennt. Ein weiterer Vorteil der kleinen Flammen in der Kammer ist die höhere Sicherheit gegen Flammenrückschlag, sodass solche Brennkammern in entsprechender Skalierung nicht nur für stationäre Gasturbinen sondern auch für Anwendungen in der Luftfahrt geeignet sind.
Die Fertigung von MMX-Brennkammern ist jedoch technisch sehr anspruchsvoll, denn die Fertigungstoleranzen sind gering: Der Betrieb einer solchen Brennkammer mit dem flüchtigen Wasserstoffgas erfordert es, dass das System dauerhaft dicht bleibt. Außerdem müssen alle Funktionselemente im Inneren der Kammer, wie etwa die Luftleitbleche, präzise zueinander ausgerichtet sein, um das gewünschte Strömungsverhalten der zu- und abgeführten Gase zu gewährleisten. Eine Fertigung allein durch subtraktive Fertigungsverfahren wie Fräsen und Bohren würde solche Bauteile jedoch sehr kostspielig machen. Daher wählten die Projektpartner ein additives Verfahren zum Aufbau ihres Prototypen: Laser Powder Bed Fusion (LPBF).
LPBF: Metallischer 3D-Druck für komplexe Bauteile
LPBF ist ein bekanntes additives Fertigungsverfahren, mit dem die Brennkammer aus einem Metallpulver aufgebaut werden kann. Dabei wird durch einen Mikroschweißprozess in einem Pulverbett die Querschnittfläche des Bauteils schichtweise aufgeschmolzen. Durch extrem dünne Schichtstärken gelingt es, die komplexe Bauteilgeometrie in einer hohen Auflösung herzustellen, in der viele Funktionselemente im Inneren der Brennkammer bereits angelegt sind. Das reduziert den Aufwand zur Nachbearbeitung deutlich.
Nach der additiven Fertigung der Brennkammer und dem Abtrennen der Plattform, auf der sie aufgebaut wurde, sind nur noch wenige subtraktive Nachbearbeitungsschritte durch Fräsen und Bohren erforderlich: So werden etwa die filigranen, beweglichen Luftleitbleche in einem Fräsprozess hergestellt und die Bohrungen für den Wasserstoffaustritt nachträglich hinzugefügt. In der Kombination der einzelnen Fertigungsschritte gelingt es den drei Partnern, die Schwächen der bisher bestehenden Verfahren zu kompensieren und die Einzelprozesse zu einer synergetischen Prozesskette zu verbinden.
Additiver Aufbau der MMX-Brennkammer verspricht bis zu 90 Prozent Kosteneinsparung in der Fertigung
Das MMX-Konzept hat sich im Testbetrieb bereits bewährt. Auf der Grundlage von Simulationen prognostizieren die Aachener Forscher zudem, dass der Einsatz von LPBF den Zeitaufwand der Montage deutlich verringern und die Kosten einer solchen Brennkammer bis zu 90 Prozent reduzieren kann. Neben den ökologischen und ökonomischen Vorteilen, die die neue Brennkammertechnologie ohnehin bietet, werden durch das LPBF-Verfahren auch die Fertigungsprozesse nachhaltiger und erfordern einen geringeren Ressourceneinsatz als die konventionelle Herstellung aus Einzelkomponenten, die aufwändig und unter vergleichsweise hohem Materialverbrauch zusammengefügt werden müssen.
Einen ersten funktionsfähigen Prototypen der MMX-Brennkammer sowie verschiedene weitere Bauteile, die mit dem LPBF-Verfahren und durch »Express Wire Coil Cladding«, ein Verfahren des drahtbasierten Laserauftragschweißens hergestellt wurden, zeigt das Fraunhofer IPT vom 16. bis 19. November auf der Formnext in Frankfurt am Gemeinschaftsstand der Fraunhofer-Gesellschaft in Halle 12, Stand D41.
Projektpartner
- Fraunhofer-Institut für Produktionstechnologie IPT, Aachen
- FH Aachen – University of Applied Sciences, Aachen
- Präwest Präzisionswerkstätten Dr.-Ing. Heinz-Rudolf Jung GmbH & Co. KG, Bremen
Video: Additiv gefertigte Brennkammer für den nachhaltigen Einsatz von Wasserstoff
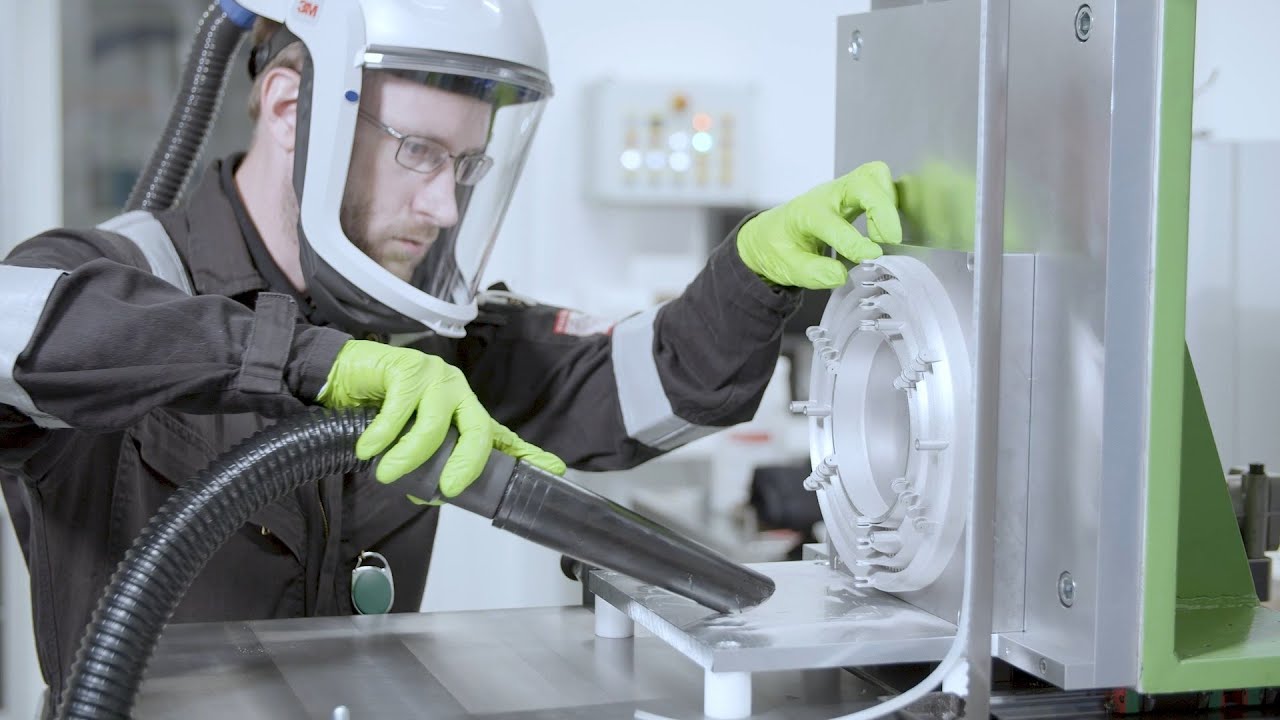