Additiv gefertigte Wasserstoff-Brennkammer im MicroMix-Design
In einem internen Forschungsprojekt haben die FH Aachen, das Fraunhofer IPT und die Präwest GmbH einen Prototypen einer additiv gefertigten Wasserstoff-Brennkammer hergestellt. Das Besondere ist das Design der Brennkammer: Das patentierte MicroMix-Verfahren verwendet im Vergleich zu herkömmlichen Verbrennungsprozessen mit einigen großen Flammen viele kleine Flammen. Dadurch wird der Ausstoß von Stickoxiden (NOx) deutlich reduziert bis auf das Niveau der fossilen Verbrennung.
Klimawandel und globale Erwärmung sind große Herausforderungen, denen sich die Gesellschaft stellen muss. Wasserstoff (H2) wird als Energieträger eine wichtige Rolle einnehmen, da die Wasserstoffverbrennung kein Kohlenstoffdioxid (CO2) produziert. Allerdings entstehen dabei mehr Stickoxide (NOx) als bei der Verbrennung fossiler Brennstoffe. Eine Neuauslegung des Wasserstoffverbrennungsprozesses mit verminderter Nox-Produktion ist notwendig; rasch einsetzbare Lösungen sind gefragt.
In einem internen Forschungsprojekt haben die FH Aachen, das Fraunhofer IPT und die Präwest GmbH eine Plug-In-Lösung für bestehende Systeme entwickelt. Gemeinsam haben die Partner den Prototypen einer additiv gefertigten Wasserstoff-Brennkammer hergestellt
MicroMix: Geringerer NOx-Ausstoß dank vieler kleiner Flammen
Die Wasserstoff-Brennkammer verfügt über das patentierte MicroMix-Design. Bei diesem kommen im Vergleich zu herkömmlichen Verbrennungsprozessen mit einigen großen Flammen viele kleine Flammen zum Einsatz. Das reduziert den Ausstoß von Stickoxiden auf das Niveau der fossilen Verbrennung. Die MMX-Brennkammer ist so konzipiert, dass das Gas optimal strömen kann und es nahezu keine Totwassergebiete gibt. Die äußere Geometrie unterstützt das Strömungsverhalten der Flammringe zusätzlich.
Das MMX-Konzept hat sich bereits in ersten Betriebsversuchen bewährt. Doch die Fertigung von MMX-Brennkammern stellt hohe Anforderungen an die Fertigungstoleranzen, die spätere Dichtigkeit sowie die Verteilung des Wasserstoffs und ist mit subtraktiven Verfahren sehr teuer.
Einfachere und kostengünstigere Fertigung einer dichteren Brennkammer
In dem gemeinsamen Forschungsprojekt nutzen die Partner zur Herstellung der Brennkammer mit der Laser Powder Bed Fusion (LPBF) ein Additives Fertigungsverfahren. Mit dem LPBF kann die Brennkammer als Integralbauteil gefertigt werden und alle Funktionselemente, etwa die Luftleitbleche, sind bereits vollständig zueinander ausgerichtet. Darüber hinaus ist der Aufwand zur anschließenden Bohrung der Speichenzentrierung bei der LPBF-Fertigung deutlich geringer.
Simulationen haben gezeigt, dass der Einsatz von LPBF die Kosten und die Montagezeit einer solchen Brennkammer um bis zu 90 Prozent reduzieren kann. In den nächsten Schritten wollen die Projektpartner den Fertigungsprozess noch weiter ausarbeiten, um weitere Synergieeffekte zu erzielen.
Synergetische Fertigungskette verbindet additive und subtraktive Verfahren
Nach der additiven Fertigung der Brennkammer und dem Abtrennen der Plattform, auf der sie aufgebaut wurde, wird das Bauteil noch weiter bearbeitet: So werden etwa die filigranen, beweglichen Luftleitbleche und die Bohrungen für den Wasserstoffaustritt in einem Fräsprozess hergestellt.
In der Kooperation gelingt es den drei Partnern, die Defizite der bestehenden Fertigungsmethoden zu überwinden und die unterschiedlichen Fertigungsprozesse synergetisch zu einer verbesserten Prozesskette zu verbinden. Die subtraktiven Fertigungsprozesse wie etwa das Fräsen oder das Bohren werden so ausgelegt, dass sie bei Bedarf entlang der gesamten Prozesskette eingesetzt werden können. All diese Maßnahmen führen dazu, dass neben dem ökologisch und ökonomisch günstigeren Einsatz der Brennkammer auch der Fertigungsprozess nachhaltiger und mit minimalem Ressourceneinsatz verbunden ist.
Partner
- Fraunhofer-Institut für Produktionstechnologie IPT
- FH Aachen
- Präwest Präzisionswerkstätten Dr.-Ing. Heinz-Rudolf Jung GmbH & Co. KG, Bremen
Video: Additiv gefertigte Brennkammer für den nachhaltigen Einsatz von Wasserstoff
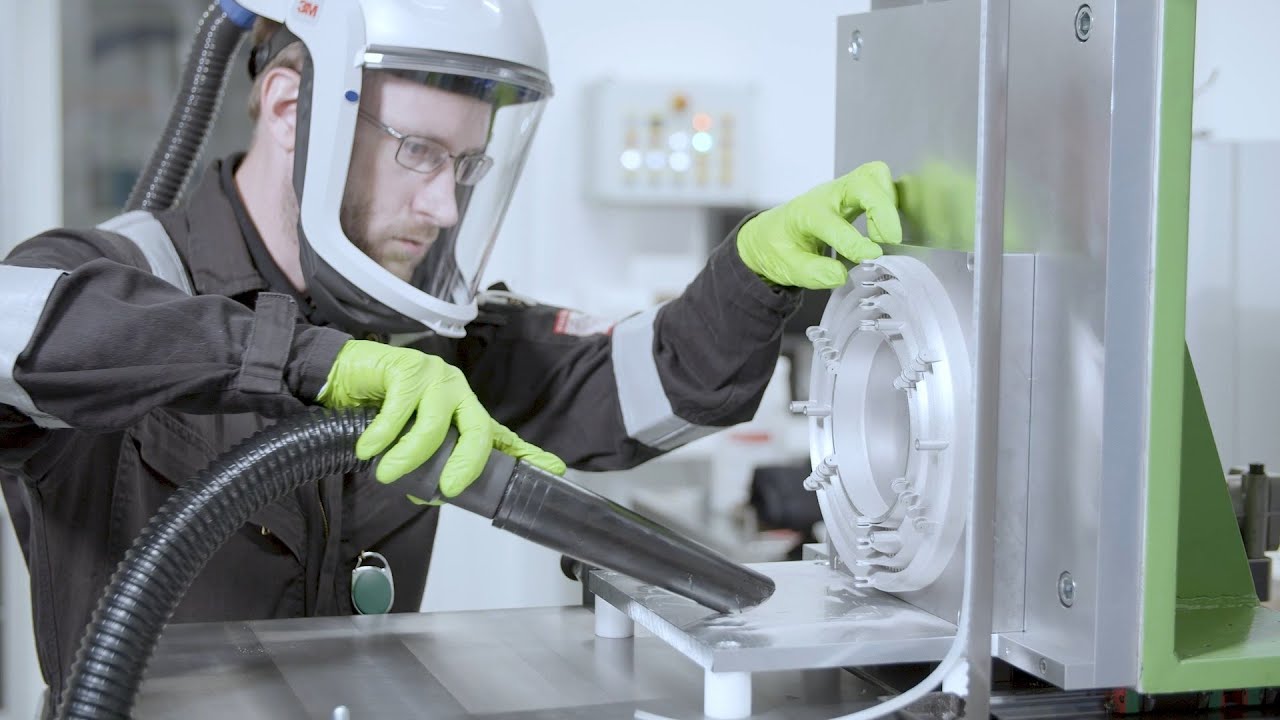