Fraunhofer Edge Cloud: Open IT test environment for research and industry
Big Data solutions require densely integrated networks of production facilities and IT – which, in turn, oblige companies to invest heavily in resources and technological skills. This is why the Fraunhofer Institute for Production Technology IPT and its project partner German Edge Cloud are currently developing an open test environment for research and industry in Aachen that will allow the testing of digitalization concepts in actual production facilities with a view to integrating these concepts into industrial production lines.
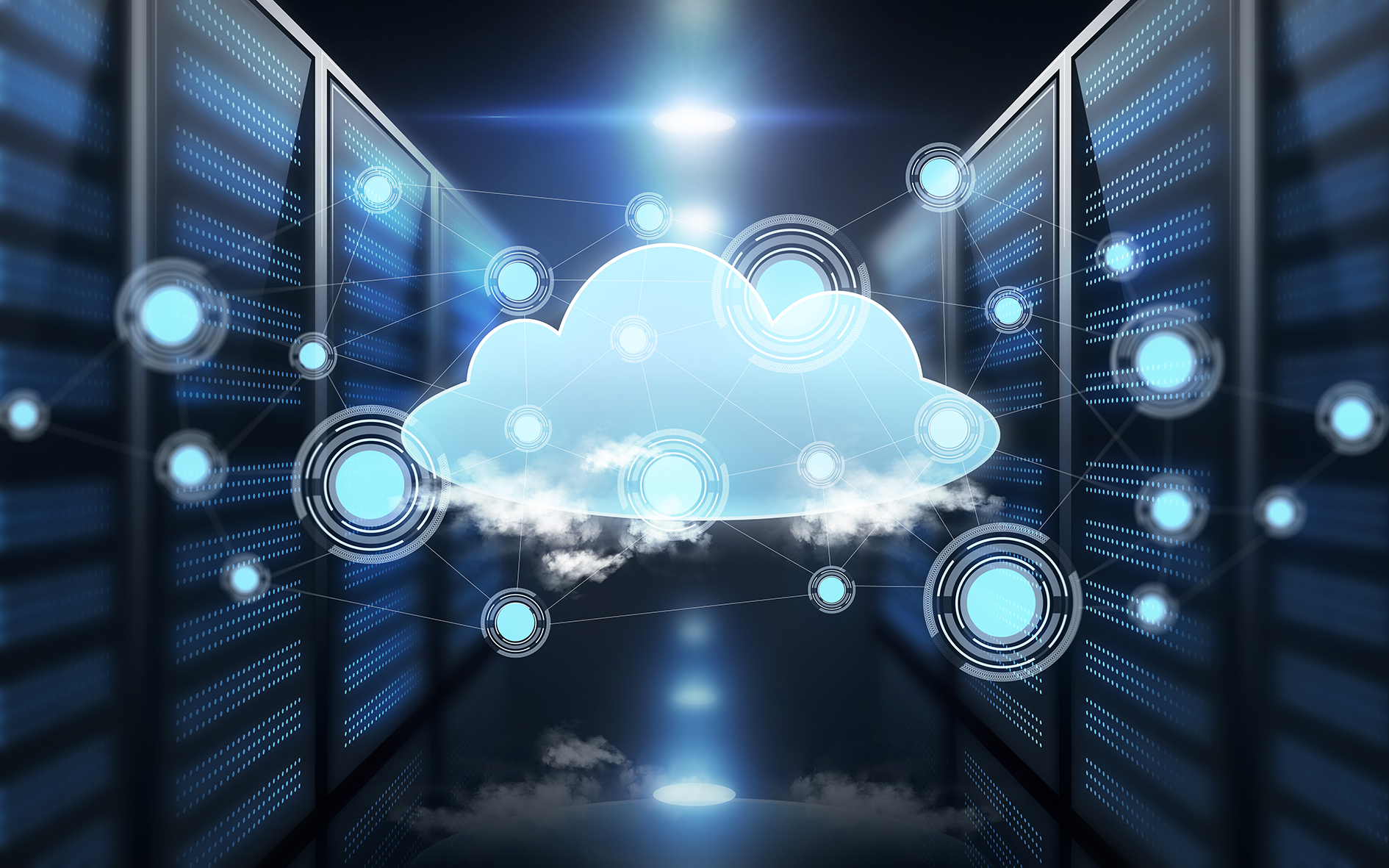
Edge cloud systems combine the technological benefits of a cloud with the data security of a company's own network. Machines and operations can be conveniently monitored, and it is relatively straightforward to subsequently optimize the production process. Intelligent sensor technology, tools for analyzing the large volumes of sensor-generated data and even machine learning applications can be connected locally to the company IT in a cost-effective manner.
The Fraunhofer IPT and the IIoT and Edge Cloud IT provider German Edge Cloud now want to launch the prototype of a scalable edge cloud environment for research and industry. The concept will also be tested by other partners inside as well as outside of the Fraunhofer community. Eventually, it will serve as a blueprint for large-scale applications in manufacturing environments or the energy industry.
Development of the production cloud for industrial applications
The joint development project is of high strategic importance for German Edge Cloud, and the company will provide the Fraunhofer IPT with the required hardware as well as full technical support services for the system. The Fraunhofer IPT chose German Edge Cloud as their preferred partner for the implementation of the Fraunhofer Edge Cloud solution, having already conducted another joint research project with the company at the "International Center for Networked, Adaptive Production". Ultimately, it was the distributed server infrastructure and the potential benefits of the open and modular platform for an industrial production environment that tipped the balance in favour of German Edge Cloud for the Aachen-based research team.
The performance of the system will be validated on the basis of practical examples from real production environments that are provided by the Fraunhofer IPT. This is meant to ensure that the Fraunhofer Edge Cloud will meet all requirements of the manufacturing industry and deliver the necessary levels of performance.
Tight schedule for a future-proof IT infrastructure
The project was launched in October 2019, and the operating system was fully installed in June 2020. Over the coming weeks, further concepts for user interfaces and networking will be implemented. The hardware of the Fraunhofer Edge Cloud is located entirely in server rooms of the Fraunhofer IPT and is connected to the network services of the Fraunhofer Gesellschaft.
The Fraunhofer Edge Cloud will be used to process virtual and decentralized projects in a structured and user-friendly manner. It has been designed to support research and industrial projects, but also to serve the internal use of IT and cloud services. The research team plans to explore and develop additional areas of application for the Edge Cloud and to set up self-developed machine learning projects or applications for distributed computing such as International Data Space, GaiaX and distributed ledger technologies.
Ultimately, the idea is to integrate the Fraunhofer Edge Cloud into a common research infrastructure for the entire Fraunhofer community, allowing more than 70 Fraunhofer Institutes in Germany and their international cooperation partners to share computing resources and process data.
First applications already in testing
Following the initial set up of the infrastructure, a first use case has been jointly performed. A so-called production cockpit was installed for cross-location analyses and further uses of measurement data from different machines and processes along the production chain. Sensor data are supported by process-related parameters, status reports about the various components and system elements, data on product quality and cost estimates. These data can then be used to improve not only the simulation models but also the forecasts of subsequent production results.